How IoT Automations Enhance Retail Warehouse Management
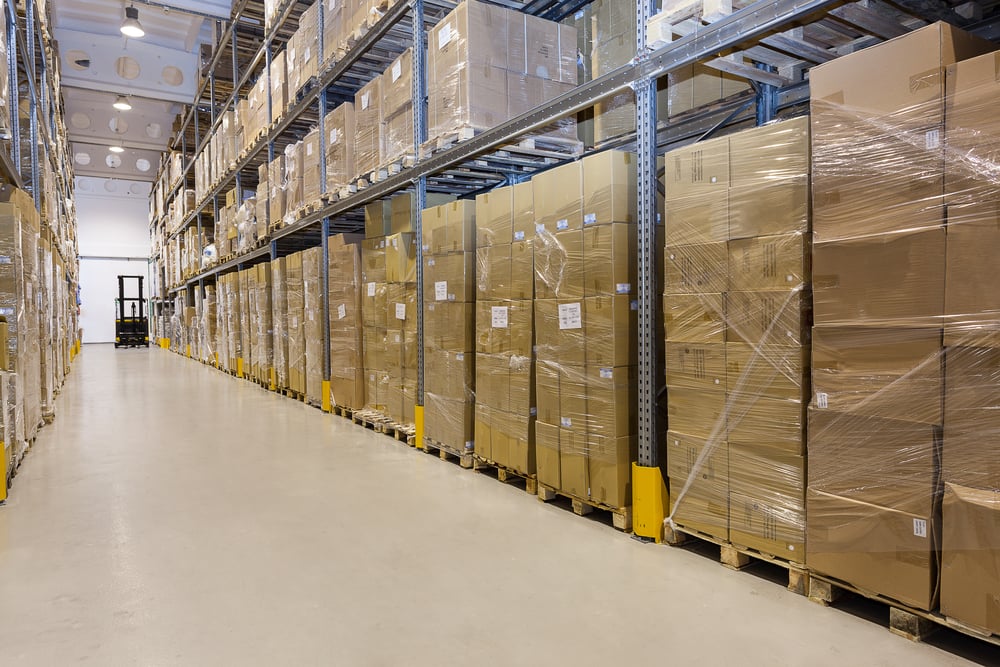
IoT systems are supporting order processing from warehouse stocks to improve customer experience using big data. These IoT warehouse management solutions allow for customers’ decisions to be tracked from products’ shelves or e-shop baskets, allowing for data to be collected and customer experience to be improved.
Why is IoT important in warehouse management?
IoT is invaluable when it comes to monitoring and streamlining the warehouse management process. This is vital for company customer service, as customers in the modern day expect from retailers a few general things such as:
- On-time delivery (with hours precision)
- Package high quality (without breaking glass in our package)
- Item(s) quality (the same thing as description and photos)
- Easy way for returning or cancel process (fast and simple processing)
- Customer support (with technical people on board)
- Better inventory management system for inventory optimization
- More efficient supply chain operations and production line
- Increase warehouse productivity
Online shopping product delivery uses continuous tracking of products to support the transport of parcels using data engineering and Internet of Things solutions. All tracking records are then stored in big data for future analytics.
Big data can help retailers with the process of warehouse management by processing the particular real time data from the data lake and then using it to perform operations.
This allows for companies to deal with an increase in product demand. Warehouse managers can extract many valuable metrics from orders based on structured and unstructured collected data like location, product ID or UUID, stock, etc. Data lakes, or delta lakes, are still in optimization to develop an agile loop.
The best part about big data is it eases the data handling and operating process. You can create dedicated data pipelines with guards and all data streams will be transformed to required business intelligence and specific machine learning formats.
It’s now possible to do something that was unthinkable a few years ago - predicting and finding anomalies in a data flow.
How to reduce errors in warehouse management processes?
Large companies use real time data streams in warehouse management systems, processing and logistics to improve their supply chain. They can use data analytics and analytical tools in a few different concepts. The big value from those concepts is the lowest error propagation and reliable work on all delivery stages.
Today's warehouse operations are very interesting from a data architecture point of view. They have algorithms, statistics, machine learning, and of course data lakes for better warehouse management.
Error predicting solutions like anomaly detections are clever ways to solve a few typical problems with warehouse management. Some solutions are based on machine learning and prediction, and it's of course a huge step to innovate today’s warehouses.
All data lakes give us more metrics but, from a business point of view, warehouses need special metrics to make better decisions. All data metrics are transformed into dedicated dashboards supporting management in doing the right decisions.
Humans use robots in warehouse operations to increase efficiency and decrease errors in delivery, such as fulfilling warehouse manager roles. This used to be a scenario from sci-fi, but today it’s non-fiction.
Retailers are investing money for extended human tools like fleets of robots, robotic arms, and exoskeletons. By having these tools at their disposal, warehouse managers can increase efficiency and customer satisfaction. The general goals in this transformation are:
- Minimizing fatigue and weariness from repetitive human activities
- Making the workplace more secure for personnel
- Extending technical limits in warehouses
Robots for rescuing warehouse management
One of the newest ways to build better logistics systems within warehouses is by using Automated Guided Vehicles (AGVs) for stock management. These are IoT warehouse management devices with dedicated mounting systems compatible with shelves present in the warehouse, and these provide some innovative commercial implementations for robotics in warehouse management.
These AGVs contain handling systems which can be used to move items throughout the warehouse or distribution center without a physical driver being present.
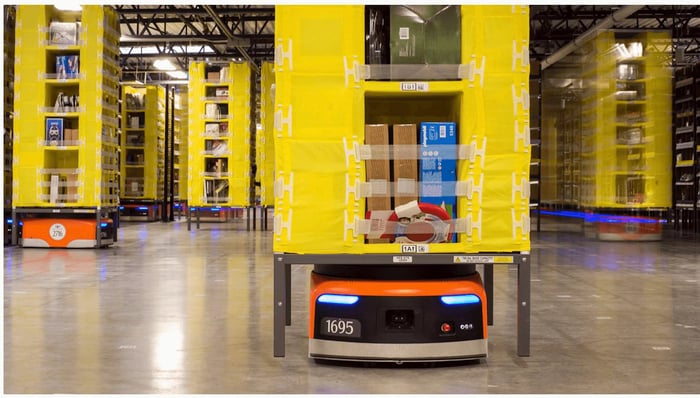
Amazon robots. Image source: Amazon Robotics
This means that AGVs can be used for tasks that would normally be done by human-operated machines such as forklifts, conveyor systems or manual carts. This automation increases the efficiency of the warehouse process via allowing AGVs to manage warehouse inventory.
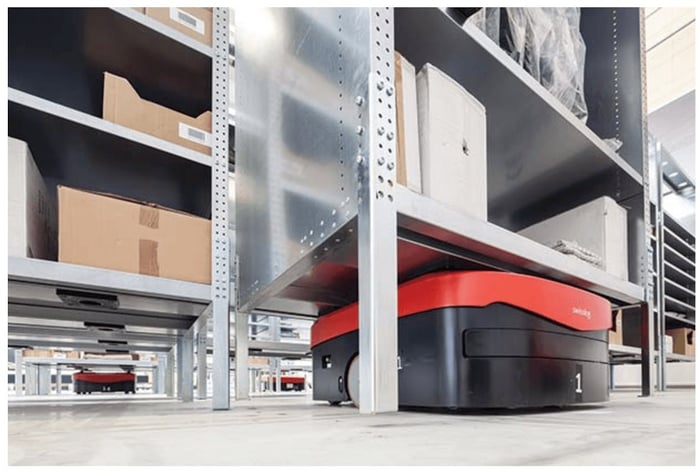
Carry Pick robot: Image source: Swisslog: KUKA
AGVs can also be used in a variety of ways. Often, they’re used for carrying materials such as metal, plastic or paper around warehouses. This would be an example of AGVs transporting these raw materials from delivery to the warehouse or from the warehouse to production lines.
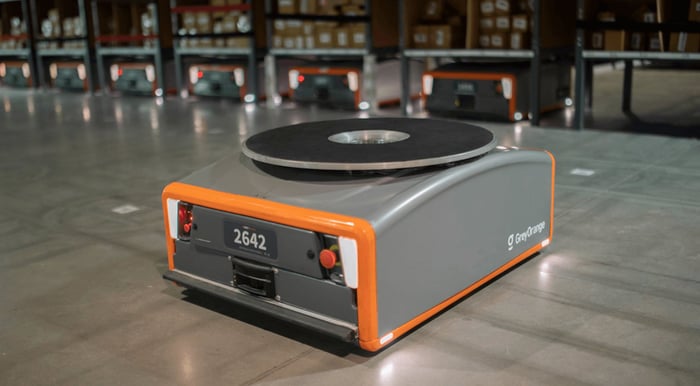
Butler robot. Image source: Grey Orange
These robots are more consistent at delivering materials quickly and safely to their destinations than human drivers, meaning production lines always have a continuous supply of materials.
As well as transporting raw materials, these robots are used within work-in-progress applications and with finished items to support production lines.
How we can build data pipelines in an autonomous warehouse
The first observation from warehouses is quasi-autonomous inside. Technical staff persons as well as a warehouse manager must be present for robotic predictive maintenance to reduce equipment malfunctions. So practically, warehouse workers and professionals are still needed inside the warehouse, and have remote connections for online experts.
These warehouse workers act more as guides for the robots to carry out the heavy lifting rather than partaking in heavy duty manual labour themselves. This allows warehouse workers to upskill and spend time doing more important, human centric jobs rather than basic labour. This creates higher employee productivity.
Based on the digital twins concept, physical experts are not needed inside because they have virtual warehouse representation with all items and connected devices, and 3D dimensions in one management/planning tool. In practice, it's the near future.
Basic example, sometimes an item from the shelf falls onto the floor. All robots need a clear workspace on the floor, so special procedures are needed to recover clear floors for AGVs. This is a simple, but typical situation. Maintenance will also be required for many fields from electronics to physical assistance.
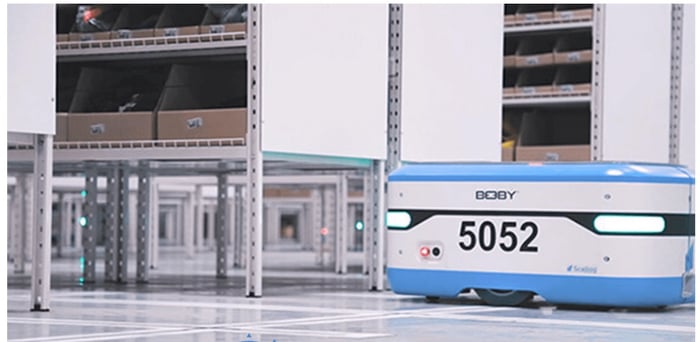
Scallog System robot. Image source: Scallog
On the other side, many retailers have been experimenting with minimizing personnel in warehouses.
Something connected with all warehouse design is that there are a lot of data streams from production IT systems (hardware and software). We can support these warehouses with data streams automation.
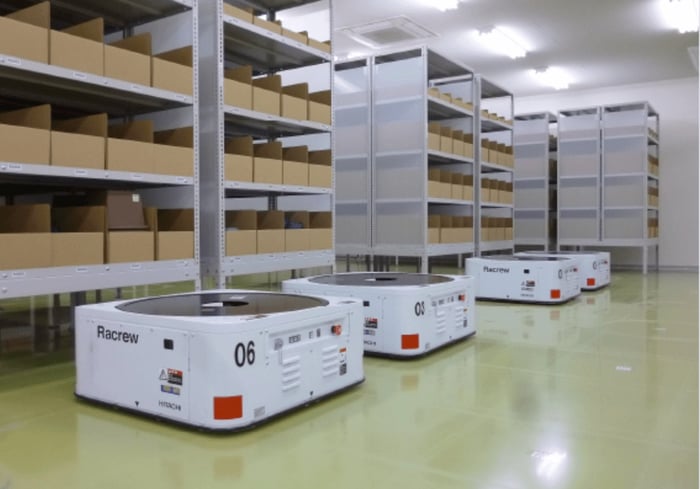
Racrew robots. Image source: Hitachi
A new way of thinking about how we can build automation in the physical warehouses is robotic fleet deployment. Not only a few arms typical for robots for pallets sorting, but thousands of middle scale vehicles with equipment for tasks such as moving the shelves.
From the Internet of Things perspective, all sensors and actuators in the robots fleet give a huge data stream in real-time. Special binary protocols like MQTT, protobuf, etc are needed for collecting data from robots. They have a two-way communication channel, so they need a good solution for a radio communication system.
Today solutions give us the possibility to develop an internal 5G network inside a factory or warehouse space for more advanced IoT warehouse management. This needs specific deployment with 5G specialists, but there is a wide spectrum of reliable options to build a mesh communication-independent system.
Modularity and reliability in a communication system for IoT warehouse management is the first point of interest. All data and commands are based on this and warehouse managers do not want signal failure from typical WiFi blockages (interferences, fields without proper signal, hidden areas, etc).
A communication system needs independent monitoring and rescue procedures. This is based on a rules system and on-call schedulers with clean defined SLA. This is a task for IT technical people.
The communication layer acts as a bridge between fleets of robots and data collecting infrastructure - data storage and data analytics. We use dedicated Internet of Things gateways and libraries from public cloud providers to develop connections with services in the cloud.
For example, MQTT protocol has full support in all public cloud providers (AWS, Azure, GCP). Sending MQTT messages is standard in IoT cores solutions and can be used with ready-to-go libraries for a lot of programming languages. In this protocol, data is organized into topics with subtopics, so data streams can be easily managed with this concept.
Digital twins give you insights into all aspects of your production line and manufacturing process. You can then use these insights to make better decisions, additionally you can automate the decision-making process with the dynamic recalibration of equipment, production lines, processes, and systems.
In practice, the robotics fleet has a virtual state in the cloud and any aspects from the state machines are mirrored in real-time between the real systems and virtual data shadows (called twins, too).
A system is built by using these IoT devices without digital twins, but if something is wrong with the physical mobile robot for a few seconds, a digital twin has the last state, and a robot after restart can fetch the current state and be ready for commands. It's a very practical solution for reliable systems because, as we know, all systems have a few seconds of unmanaged downtimes every now and again.
This is normal and digital twins can rescue you from spending hours with debugging problems. For example, if you have 3000 robots you have tens of micro downtimes per minute. It’s impossible to manage this incident by technical stuff. This architecture is needed to simplify maintenance and faster data collecting from robot fleets.
If you have an IoT technology layer fully managed with IoT cores, you have the next step in our data pipelines. That step is its data transformation and routing rules. This step is needed because all the data from the Internet of Things systems requires processing with business intelligence solutions.
When you build information trees with categories of data, all you need to do is connect all the data with a data streaming system for faster analytics. There are a few examples for doing this job from the public clouds like:
This is the level when data is normalized or denormalized, based on destination expectations. Reports can be built reports from data streams mixed with other analytics data.
This is the level when all data is transforming into dedicated dimensions and tables.
Using those tables on the next level of our pipelines, business intelligence tools or machine learning solutions, can give us the results we need.
For example - we have a data warehouse or data streams from our robotic warehouse to track data. This is the right place for discussion about reports, dashboards, and monitoring. Our BI and ML specialists can do this job very well with data engineers.
Today solutions examples from IoT enabled warehouses
Here are several examples of different IoT solutions enhancing warehouse management.
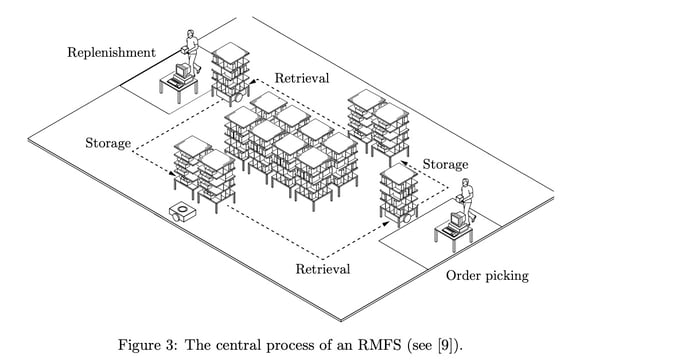
The central process in a warehouse with sorting items automation. Image source: From Simulation to Real-World Robotic Mobile Fulfillment Systems
Amazon’s sorting facility
Packages going to people with the help of robots in Amazon’s sorting facility. As we can see in the below photo, the robot is moving shelves with items. Amazon’s robotic fleet is cooperating with personnel in the sorting facility center to maximise tasks such as inventory management and other inventory processes.
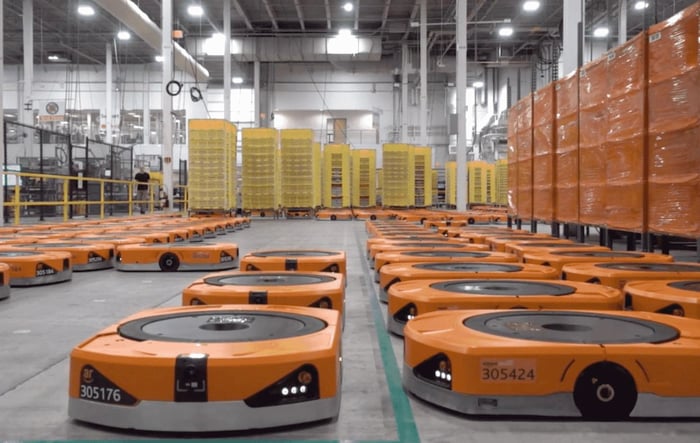
Amazon robots. Image source: Waredock
Not all tasks are for autonomous mobile robots, a few tasks are from human hands, creating a semi-automated warehouse. For something with a huge delivery process, a smart warehouse with special IoT devices, in this case a fleet of robots, is a perfect design that creates an incredibly efficient supply chain network.
Ocado’s automated, smart warehouse
This fully robotic warehouse, using a hive-grid-machine (see in Fig 4) and IoT technologies is the creation of Ocado, a British online-only supermarket that’s made a name for itself in recent years designing highly automated, smart warehouses and selling the tech to other grocery chains.
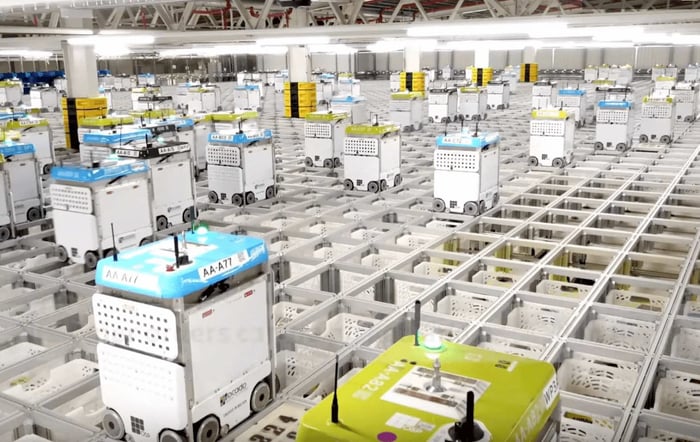
Ocado warehouse robot. Image source: New Atlas
These smart warehouse technologies are vital for running operations in modern, intelligent warehouses. When fully completed, Ocado’s operation is set to be its most advanced yet, processing 3.5 million items every single week. It’s also a perfect example of the wave of automation slowly hitting the supply chain of countries around the world.
Individually, the bots aren’t intelligent; they don’t make decisions for themselves. But their actions are all coordinated by central infrastructure. All the data is collected in one place and dedicated algorithms supporting decision-making, next sending commands to bot. There is a special place for repairing robots inside and testing sandboxes for verifying before Ocado’s bot is switch into production mode.
Benefits of robotics warehouses
Robotics offers interesting benefits in warehousing and manufacturing, too. These robots increase the efficiency of supply chains by carrying out basic tasks using supply chain data and, by analysing and using data streams, predictive maintenance can be carried out to make sure the robots run as smoothly as possible.
Increase efficiency and productivity
Because they operate autonomously, AGVs can increase the efficiency of a supply chain, and they’re predictable and reliable for repetitive tasks. AGVs eliminate unnecessary walking and also eliminate the physical labor of transporting materials. They set the pace for workers as well, keeping associates on-task.
AGVs guide human workers through each task, reducing human error and helping to improve order accuracy by minimizing loss and misplaced products. By leveraging artificial intelligence to optimize routes and prioritize work, collaborative robots improve resource utilization whilst inventory data analysis can be used to track inventory management and improve inventory optimization.
Consistent costs
In general, robots such as AGVs are rented on a per unit per period basis, meaning there’s less variation in costs compared to human labour. This is because human labor fluctuates based on conditions and demand.
Flexibility
Depending on the model, some robots can offer flexibility by being able to easily change pathways without requiring re-routing guide wires or other infrastructures. This means AGVs are a scalable solution with the ability to add more units on demand.
Less space required
Compared to other automation solutions, such as conveyor systems, robots require less space. Some robots are smaller compared to traditional warehouse equipment, such as forklifts, which allows for floor layouts with narrower aisles and better space utilization.
Improved safety
Finally, robots are a safe automation solution for IoT warehouse management, distribution centers, and manufacturing facilities. Robots are equipped with sensors to avoid collisions.
Advanced warehouse robots like AMRs have intelligent routing capabilities that enable them to plan the most efficient path through a warehouse or facility, reducing aisle congestion and preventing injuries.
IoT automations transforming retail warehouse management
AGVs are uniquely designed robots to automate tasks for which humans are not necessary. They automate long walks in warehouses, set the pace for workers, improve inventory management systems and eliminate the physical rigors of a traditionally physically demanding job. From a data engineering point of view, you can manage a fleet of robots and develop more optimal algorithms, low-cost routes, and more performant delivery.
Customers are satisfied when they have a package on time and with proper items - IoT technology in warehouses provides us this level of satisfaction. For warehouse owners it's a new era of thinking about data analytics, planning in logistics, and scaling warehouses into new regions.
We can support your company with difficult algorithms for analyzing all data streams from warehouses. Better monitoring gives us excellent predictive maintenance systems and, of course, delivery that customers will be happy with. You and your employees can feel safe using autonomous warehouse operations.
With the backdrop of Industry 4.0 initiatives and consumer changes, automation and robotics continue to infiltrate manufacturing environments. Researchers include forecasts to 2023 with assumptions for all market segments, with detailed discussions of the key issues and trends impacting the mobile robot market. Right now they assume 580,000+ Order-Filling Robots to Work in Warehouses by 2023.